VA Tech researchers are breaking the mold of ultra-lightweight ‘aerogels’
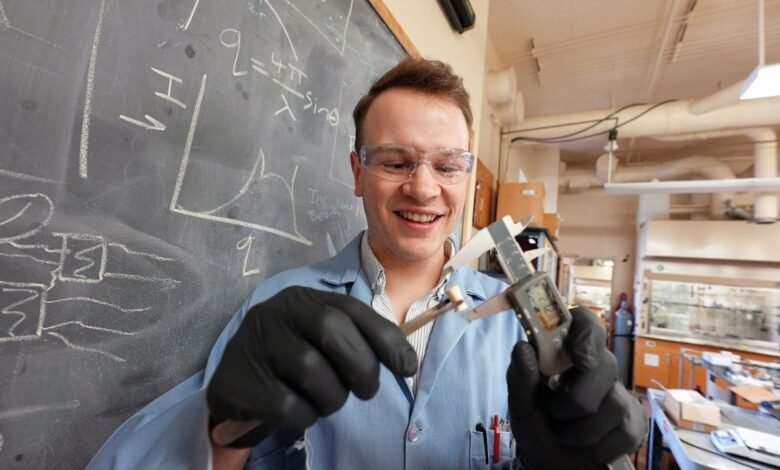
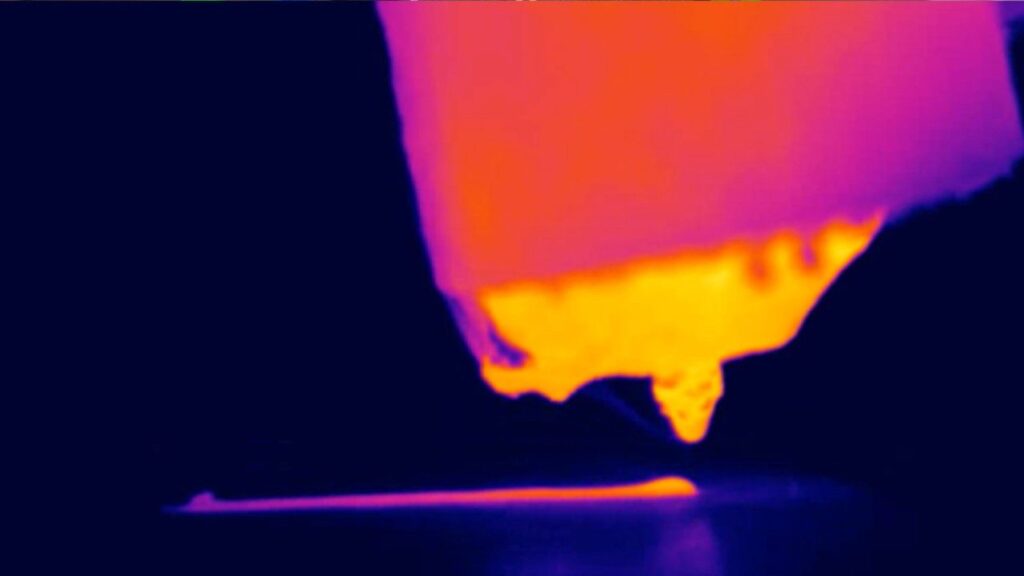
strong and light skeleton
The first step in creating an aerogel involves producing a gel, a 3D solid network that traps liquids such as water in gelatin. In the next step, the liquid inside the gel is carefully removed, leaving behind a microporous, spongy skeleton. This skeleton is ultra-light due to the replacement of heavy liquid with air, and potentially strong due to the interconnected 3D lattice.
One material that has not previously been developed as an aerogel is polyphenylene sulfide (PPS). It is an ultra-strong thermoplastic that is often used as a replacement for metal when weight savings and chemical resistance are required. As an aerogel, PPS could lead to a new wave of applications, especially in lightweight high-performance insulation. Recently, Moore’s research group demonstrated a simple process to create his PPS gels and aerogels using proprietary non-toxic and environmentally friendly solvents.
Moore’s team took the process to Williams, who is pioneering new 3D printing methods.
“Bob and I have collaborated for many years because of the interdisciplinarity fostered through the Polymer Innovation Institute,” Williams said. “We hosted a joint meeting between the two groups over the summer so that students could become more aware of the capabilities and expertise of our lab and ideate ways we could collaborate. From that meeting , I found that Bob’s new approach to synthesizing PPS airgel blended well with my group’s expertise in 3D printing and previous research in PPS printing.”
“Unlike silica aerogels and other cross-linked polymers used by NASA, our PPS gels do not require complex chemical reactions and can be melted and solidified over and over again,” Moore said. I am. “All we have to do is make a hot solution of commercially available PPS and let it cool to room temperature. When used, the PPS solution gels in seconds. It’s as easy as making Jell-O. But after seeing these gels solidify super fast, we’ve teamed up with Williams’ group to make this possible to print. I decided it was time to find out.”
The PPS airgel barrier was broken with Moore’s discovery of rapid PPS gelation. A combination of simple chemistry and his 3D printing innovations resulted in the first additive manufacturing of PPS to aerogel.
break the mold
Similar to gelatin, the gels used to make aerogels are traditionally formed in open molds. This results in a solid form with limited size and shape. Producing his PPS airgel with engineered shapes and geometries requires a combination of innovation in polymer chemistry and advanced manufacturing.
For Moore’s team, Godshall created pellets of PPS gel and placed them in a new high-temperature printing tool that Lau designed specifically for this task. Inside the nozzle, the gel pellet is reliquefied and extruded onto a substrate, where it cools and resolidifies.
After printing, the solvent-containing gel part is replaced and freeze-dried to remove the solvent, resulting in PPS airgel. This process allows for the formation of fine pores that can be adjusted through print settings. Furthermore, at the macroscale, the three-dimensional shape of PPS airgel can be tailored through the infinite shape possibilities of 3D printing.
Creating large, lightweight shapes to match the contours of airplane wings, or small insulating structures built into electronic devices, means less material in manufacturing. Strong airgel frameworks could equate to fuel savings through lighter vehicle weights, and engineered insulation could improve the energy efficiency of next-generation technologies.
“This publication represents a significant advance in the production of complex aerogels from engineered polymers,” said Williams. “Bob’s synthesis technique can also be used with many other high-performance polymers, and the printing process can be easily modified to accommodate these changes. We were surprised to learn this and are excited to study this further and discover how to control and program this structure and performance into new multifunctional parts.”
Written by Alex Parrish
Source link