Four founders talk about the future of construction technology
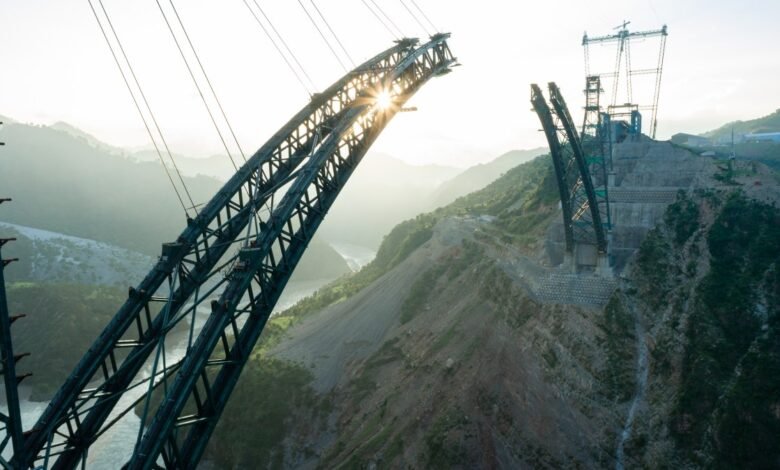
Image credits: Retina Charmer Productions/Getty Images
Employers and employees alike are watching closely to see how the future of work is shaping up. In many fields, when we read about the future of work, images of remote work and Zoom meetings come to mind. However, this is not the case in the construction industry. The construction industry is one industry where remote work is not realistically possible. The construction industry is also stuck in old ways, with little process updating or new technology implementation.
That doesn’t mean the construction industry is completely avoiding new ways of doing things. The phrase “move fast and break things” may not be something you want to use in connection with construction, but when innovation brings a lot of positives while minimizing the negatives, you can’t ignore it. . Even when problems are too big to avoid, the industry has shown a willingness to rely on cutting-edge technology to find solutions.
Over the next few days, we’ll take a deep dive into what the future of construction work will look like. To build more context about it, we’re taking an overview of construction technology trends to get a basic idea of where the industry is heading. We spoke to several construction technology founders to share their vision for the sector.
Who we spoke to:
Ritwik Pavan, Founder and CEO of Krava
James Swanston, Voyage Control Founder and CEO
Constantin Kaufmann, Co-founder and CEO of Oculai
Yosh Rozen, PartRunner Founder and CEO
Answers have been edited for length and clarity.
Ritwik Pavan, Founder and CEO of Krava
How will the construction industry change in 2030? What early technologies do you expect to be commonplace by then?
I believe that by 2030, several aspects of the construction industry will be fully digital and automated. Technologies such as drones for field surveying, his AI for design optimization, and robots for tasks such as bricklaying and concrete pouring are likely to become the norm. Additionally, augmented reality could play a role in real-time project visualization, and advanced 3D printing could also enable rapid prototyping and manufacturing of full-scale architectural components.
Other than labor shortages in certain markets, what do you feel is ripe for disruption in the construction industry? What have you done to take advantage of this?
Beyond labor shortages, there will be significant disruption to the construction industry’s supply chain management and ordering processes, especially for custom materials and components. ADUs offer a unique opportunity, one that Krava is strategically leveraging. By improving and creating standardized processes and leveraging technology, construction supply chains can become more efficient, predictable, and customizable.
Given that the construction industry can be reluctant to adopt new technology, how easy has it been to move forward in the market? What lessons have you learned from other players who have struggled to make their mark?
Our initial focus on homeowners and the burgeoning ADU market allowed us to overcome the traditional construction industry’s hesitancy toward new technology. By proving our technology and processes on a small scale, we are building a compelling case for developers at scale. History shows that disruptive players often face resistance, but consistent results, adaptability, and an understanding of market needs can pave the way for acceptance.
Do you think there will be major changes in the way the construction process operates in 2030? Will the industry undergo a meaningful evolution?
By 2030, we expect the majority of residential construction to shift to industrial construction. The main reason is that we don’t have a choice. Current building methods are simply not equipped to handle the looming housing crisis and the speed at which homes are being built. Manufactured buildings, modular setups and streamlined supply chains will be crucial to efficiently meet housing demand. I believe the industry won’t just evolve. It will undergo a major transformation, reshaping how we perceive and approach the very concept of construction.
Founder and CEO James Swanston navigation control
How will the construction industry change in 2030? What early technologies are you doing? Do you think it will be common by then?
By 2030, we hope that data integrity will be better than it is today. The industry still needs to move from simply collecting data to properly analyzing it to make better decisions. Most technology companies try to help their customers with this, but it’s a daunting task.
Other than labor shortages in certain markets, what do you feel is ripe for disruption in the construction industry? What have you done to take advantage of this?
There are significant macro trends surrounding ESG, whether through regulatory mechanisms such as the proposed FAR. [Federal Acquisition Regulation] U.S. Judgments or Stockholder Expectations and Obligations. Ultimately, the companies that will have the most impact are those that finance and insure construction projects. We are in the fortunate position of working with many clients to help them think about how to better manage their supply chains. ESG is an important part of that.
Given that the construction industry can be reluctant to adopt new technology, how easy has it been to move forward in the market? What lessons have you learned from other players who have struggled to make their mark?
Gaining trust can take time, but we were fortunate to find many innovators and early adopters around the world with whom we were able to partner. But fundamentally, this is all about behavior change, and it’s a long game. The big lesson is to not get too far ahead of the market so your customers can truly understand their ROI and grow in improving efficiency through technology.
Do you think there will be major changes in the way the construction process operates in 2030? Will the industry undergo a meaningful evolution?
I don’t think the supply of manual workers will be able to keep up with the demand. This will lead to increased use of technology and robots, as well as a focus on reducing inefficient and time-consuming processes. Another big change is the focus on his supply chain, either as a result of operational needs or his ESG obligations.
Constantin Kaufmann, Co-founder and CEO of Oculai
How will the construction industry change in 2030? What early technologies do you expect to be commonplace by then?
Until 2030, we won’t see much change on the ground, except for advanced prefabrication. However, the digitalization of site management and planning will continue to advance. An upcoming trend is the use of AI techniques in the construction field, such as computer vision (e.g. progress and process tracking) and language processing (e.g. scanning and interpreting delivery documents).
I hope that Excel and paper will be replaced as document creation tools by 2030.
Other than labor shortages in certain markets, what do you feel is ripe for disruption in the construction industry? What have you done to take advantage of this?
Many construction companies (especially in Germany) do not have defined standards that apply to all projects within the company. In these cases, the project manager uses her own set of tools, suppliers, subcontractors, and obtains her own experience and data. Defining standards allows data and knowledge to be exchanged and maximizes value in the field.
The value of the data collected is greatest as more projects are tracked. We encourage users to increase the size of their database to generate comparable reference values for subsequent projects to more accurately measure efficiency.
Given that the construction industry can be reluctant to adopt new technology, how easy has it been to move forward in the market? What lessons have you learned from other players who have struggled to make their mark?
One of the challenges that Contech startups face is project-based business. Many construction companies handle each project independently, and there are few established company-wide standards. As a decentralized business, there is no centralized structure. We found that implementing the solution across all construction sites was time consuming and required buy-in from both users and leaders.
Another challenge is establishing new processes for new sources of information. We have found that without support during implementation, data alone cannot be utilized or translated into action. We learned that we need to stay in close contact with our users and show them how to use their data for tangible benefits.
Do you think there will be major changes in the way the construction process operates in 2030? Will the industry undergo a meaningful evolution?
I think the construction process will be much the same as it is now, with more prefabrication. I think the industry, especially project management, will rely more on data and less on emotion. We have seen that process data is a key driver of process improvement and decision-making in the manufacturing industry and can unlock huge potential in the construction sector.
Yos Rosen, Founder and CEO, Part-time runner
How will the construction industry change in 2030? What early technologies do you expect to be commonplace by then?
Technologies that make the construction industry more efficient:
- sustainability: Materials, transportation, construction, carbon footprint, etc.
- Digital transformation: Operations “act” as data models that use ML and AI to make processes more efficient.
- IoT: A smart device that collects data on vehicles, equipment, tools, etc. to improve the lifespan and maintenance of products, materials, equipment, etc.
- logistics: Speed, quality, reliability, cost.
Given that the construction industry can be reluctant to adopt new technology, how easy has it been to move forward in the market? What lessons have you learned from other players who have struggled to make their mark?
we have worked very close [with] Decision makers at all levels, from small businesses to large corporations.understand their needs [and] We deliver direct value to our customers by supporting solutions that solve challenges and create value in the way we do things internally.
- Increase profits.
- Reduce costs.
Lesson:
- It requires a consultative approach to building pilots, understanding needs, testing hypotheses, and continually reviewing metrics and feedback.
- Embrace a culture of innovation consisting of internal innovation (literally building internal innovation teams) and external innovation (via startups and new technologies).
assignment:
- Change management.
- Change your way of thinking.
- Learning curve.
- Risk and adversity due to “not knowing”.
- Legacy processes and systems.
Do you think there will be major changes in the way the construction process operates in 2030? Will the industry undergo a meaningful evolution?
Technology is advancing faster and exponentially than ever before.
There will be major changes in the coming years through AI, ML, robots, IoT, marketplaces, and fintech solutions. It’s like a tsunami. I know it’s coming and I know I’ll have to deal with it at some point. You have to start learning how to surf and ride when the waves come.
The best companies are those that embrace this change and make the necessary changes across the company to remain adaptable and embrace innovation.
Source link